Description of the model
The purpose was to implement if possible a rack-and-pinon steering mechanism with the usual Ackermann trapezium as geometry.
The difficulty is to set axles at an angle, since the orientation of Lego axles is fixed.
I built the model first with real parts, in at least four iterations. The first two used modified parts: a ball joint link at 90º and two quarter bushings, neither of which exist as standard Lego parts. As this was no good for publication to readers who might wish to built their own instances, I used the second two iterations to come up with a model that can be built. The test here is that it must be possible to make it in LDD (Lego Digital Designer).
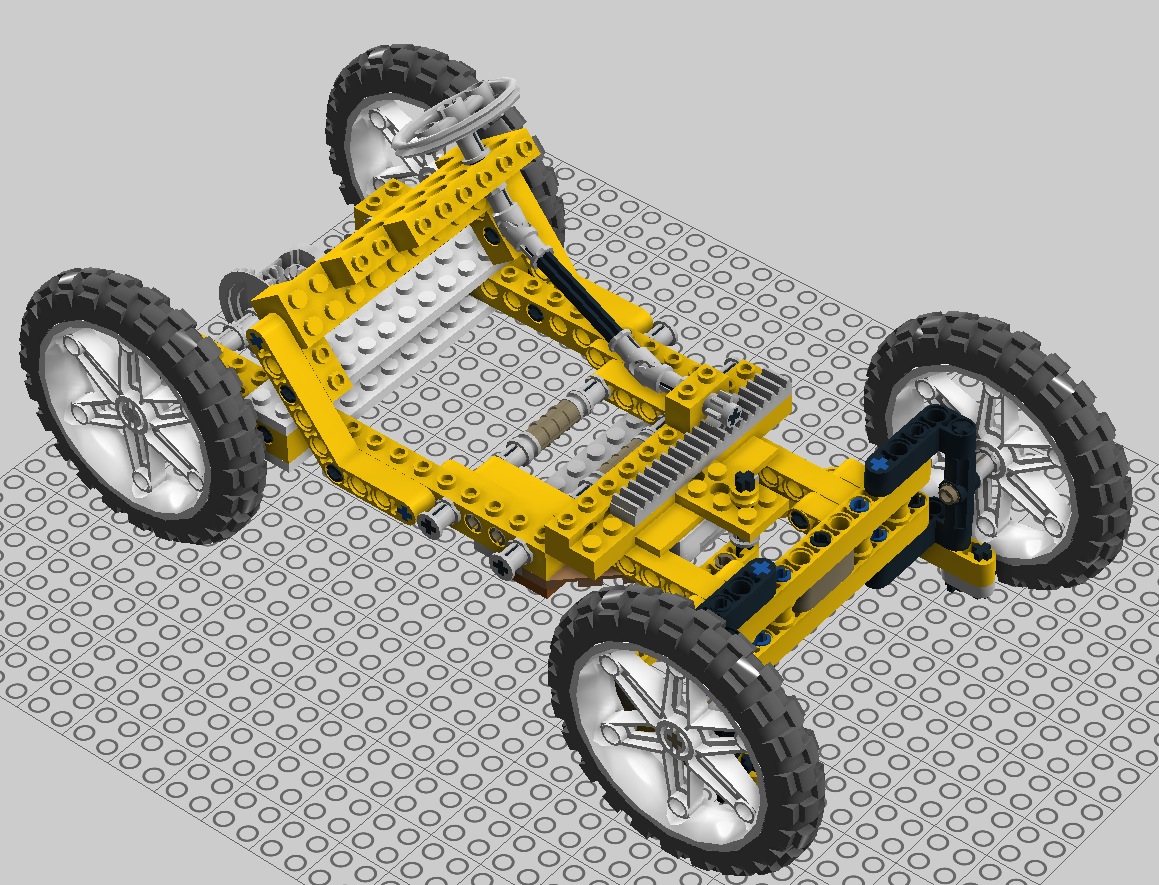
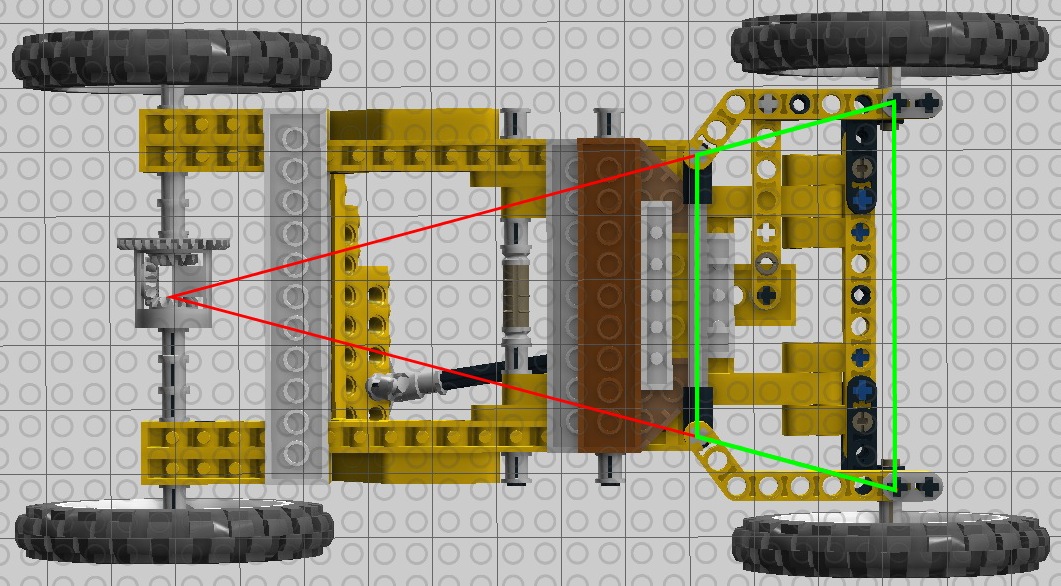
Please do not call this model a MOC: it has no other merit than to show that the trapezium geometry of the Ackerman steering is possible.
I spent no attention to ruggedness and certainly none to good looks, so it is futile to criticise it.
Those who wish can download the lxf file and in “Building Guide Mode” see how it was done.